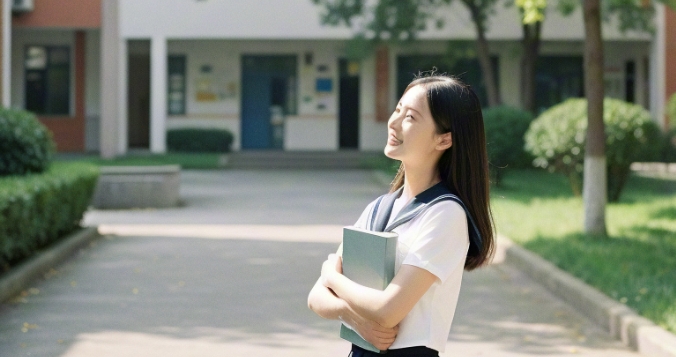
成都工业职业技术学院现代车间是西南地区职业教育领域产教融合的实践典范,其建设理念围绕“智能制造+工业互联网”展开,整合了工业机器人、数字化生产线、虚拟仿真系统等先进设备,构建了“教学-实训-研发-生产”四位一体的综合性实践平台。车间总面积超8000平方米,配备价值近5000万元的工业设备,涵盖机械加工、电气控制、智能仓储等模块,可同时容纳300名学生进行实训。通过引入企业真实生产项目,该车间实现了教学场景与产业需求的无缝对接,尤其在精密加工、工业物联网(IIoT)应用等方面形成显著特色。值得注意的是,车间采用“双导师制”,企业工程师与学校教师联合指导,显著提升学生解决复杂工程问题的能力。
一、设施配置与技术架构
现代车间的硬件设施以“智能化”为核心,包含6条柔性制造生产线、12台六轴工业机器人及全流程数字化管理系统。与传统实训车间相比,其设备集成度与技术先进性优势显著。
对比维度 | 传统实训车间 | 成都工业现代车间 |
---|---|---|
核心设备 | 普通机床、单一PLC控制台 | 工业机器人、数字孪生系统、AGV物流车 |
网络架构 | 局域网独立运行 | 5G+工业物联网全覆盖,支持远程协同 |
生产模式 | 离散型单项训练 | 混合式柔性生产,可承接企业订单 |
二、课程体系与教学创新
车间采用“项目驱动+模块化教学”模式,课程覆盖智能制造全链条。例如,通过“工业机器人编程与维护”课程,学生需完成从代码调试到故障排除的完整任务。
课程类型 | 理论占比 | 实操占比 | 企业参与度 |
---|---|---|---|
传统学科课程 | 70% | 30% | 无 |
现代车间课程 | 20% | 80% | 深度参与(标准制定、案例提供) |
三、校企合作机制
车间与西门子、富士康等企业建立“双向赋能”合作,企业提供技术标准与生产任务,学校输出技能人才与创新成果。
合作模式 | 资源投入方 | 成果归属 |
---|---|---|
订单式培养 | 企业主导设备捐赠 | 按企业需求定向输送人才 |
横向课题研发 | 校企联合资金与技术 | 共享知识产权 |
生产性实训 | 学校场地+企业订单 | 收益反哺教学设备更新 |
四、学生能力培养路径
通过“基础技能→专项技术→综合应用”三级进阶体系,学生从操作单一设备逐步过渡到主导完整生产流程。
- 初级阶段:掌握工业机器人示教、PLC编程基础
- 中级阶段:参与智能产线调试、MES系统应用
- 高级阶段:完成跨部门协作的订单任务,包含工艺优化与成本控制
五、技术研发与社会服务
车间不仅是教学场所,更是技术转化平台。近年完成“智能仓储调度算法优化”“数控机床精度补偿”等横向课题,为企业节约成本超千万元。
六、信息化管理系统
采用MES生产制造执行系统,实现实训过程全程数字化管控。学生操作记录、设备状态、质量检测数据均可追溯,为教学评价提供量化依据。
七、区域经济适配性
紧扣成渝双城经济圈制造业需求,重点服务电子信息、汽车制造等产业。2023年数据显示,毕业生对口就业率达92%,本地企业满意度超85%。
八、挑战与改进方向
当前面临设备维护成本高(年均300万元)、师资迭代压力等问题。未来计划引入AI辅助教学系统,探索“数字孪生+远程操控”新模式。
成都工业职业技术学院现代车间通过重构教育场景、深化产教融合,有效解决了传统职业教育与产业脱节的痛点。其“生产真实化、技术前沿化、教学个性化”的特点,为智能制造人才培养提供了可复制的范式。随着工业互联网与人工智能技术的迭代,车间需持续强化数据驱动的教学决策能力,并拓展国际化认证标准,以应对全球产业链升级需求。